Two nuts that are often neglected in periodic engine inspections are the propeller fastening nut and the engine thrust nut. Both require special wrenches to tighten and loosen them, and maybe for this reason they are overlooked and assumed to be properly torqued. The torque values for each nut is also an order of magnitude greater than any other fastener on the engine. However, along with all the other engine fasteners, these nuts require attention during periodic inspections.
A few years ago an aircraft whose engine that had begun showing ferrous metal in the oil came into our facility. In preparation to remove the engine from the aircraft we first began to remove the propeller. It was then that we discovered that the propeller nut was not tight on the crankshaft. It had been snugged down and safetied, but had not been tightened to the proper torque. The arrows on Figure 1 show wear on the crankshaft splines caused by the propeller chattering on the crankshaft.
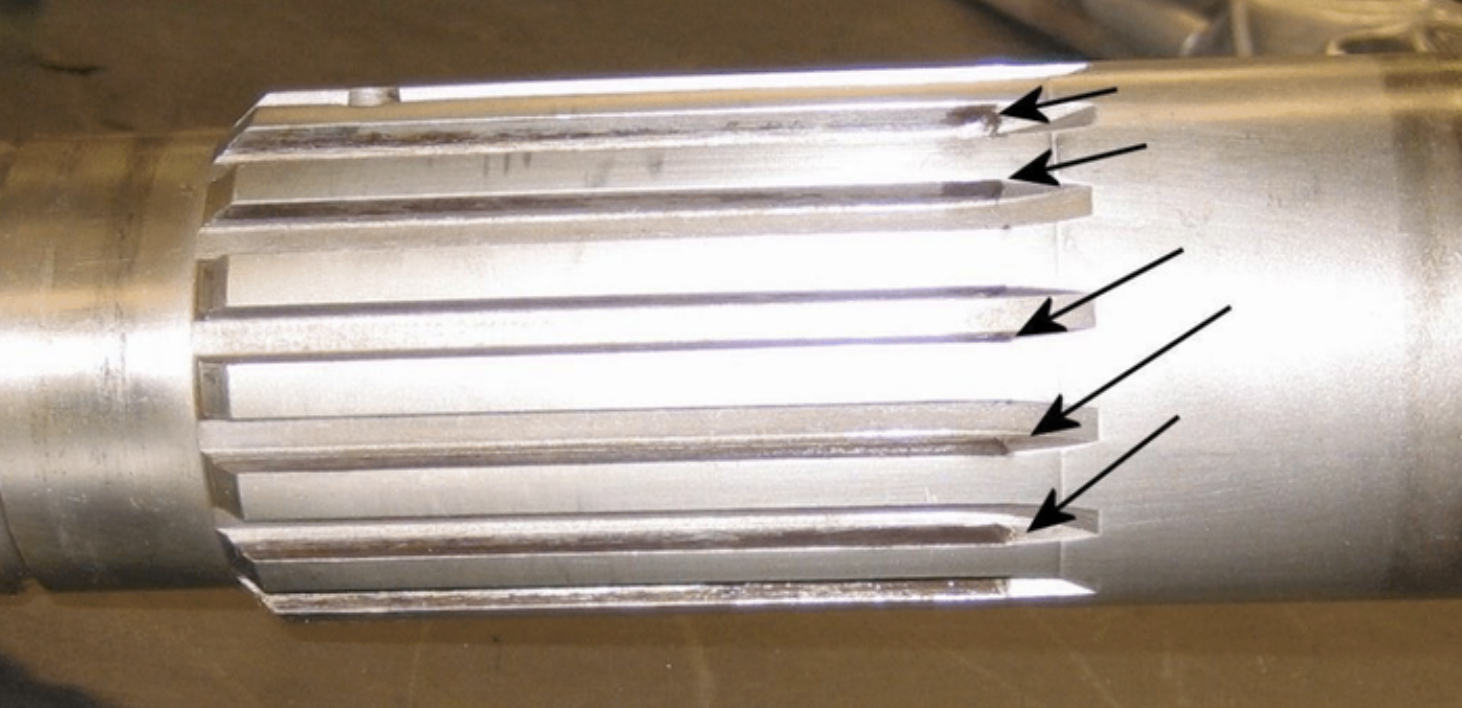
This wear was a cause of rejection for the crankshaft and was a sign of things to come as we continued to disassemble the engine. Figure 2 shows the wear caused on the inner race of the front main bearing by the loose propeller. This wear was the source of the ferrous metal that had been found in the oil.
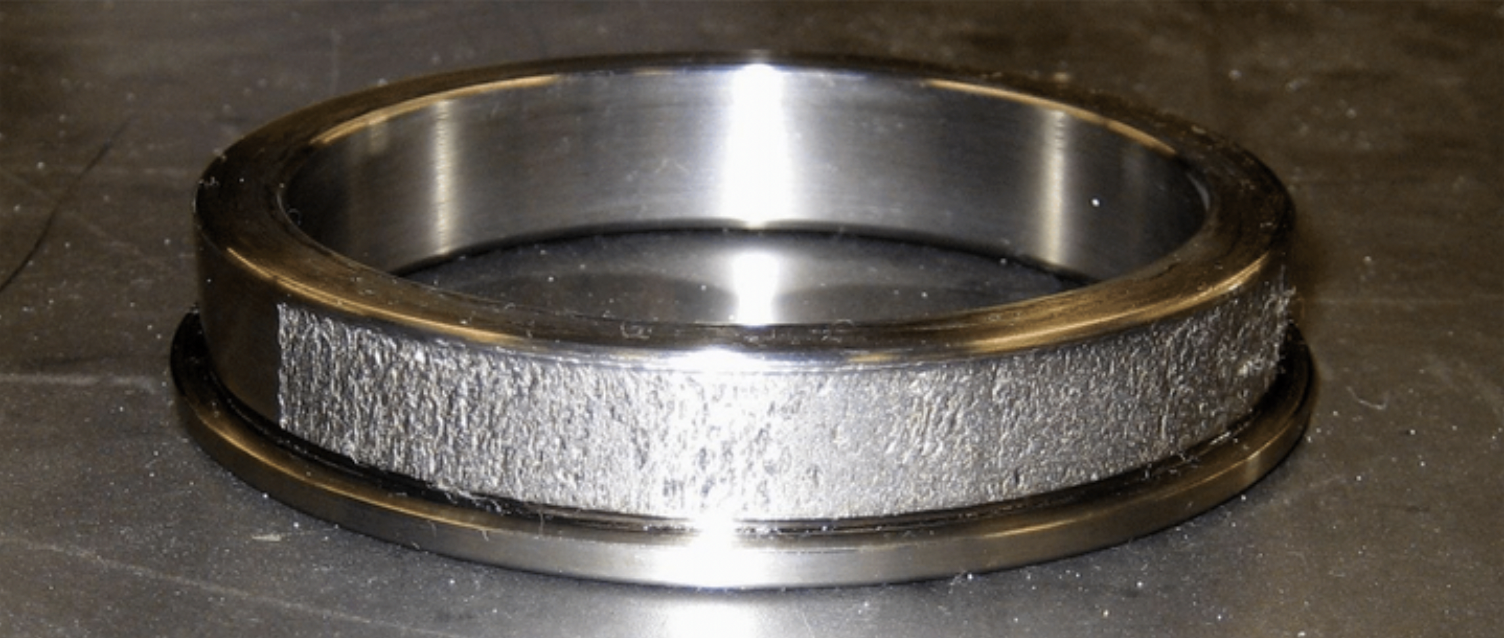
This customer was fortunate that he found the metal in the oil before further damage was done.
On another occasion a different customer experienced a total loss of engine oil pressure in flight. He was able to land the aircraft successfully and upon inspection also found ferrous metal in the oil. When we inspected the engine we noticed that the thrust nut was loose and that the crankshaft could be moved forward and after about .090”. Upon disassembly we found the crankpin had broken in two but was still clamped in the rear half of the crankshaft (Figure 3), underscoring the importance of proper thrust nut torque.
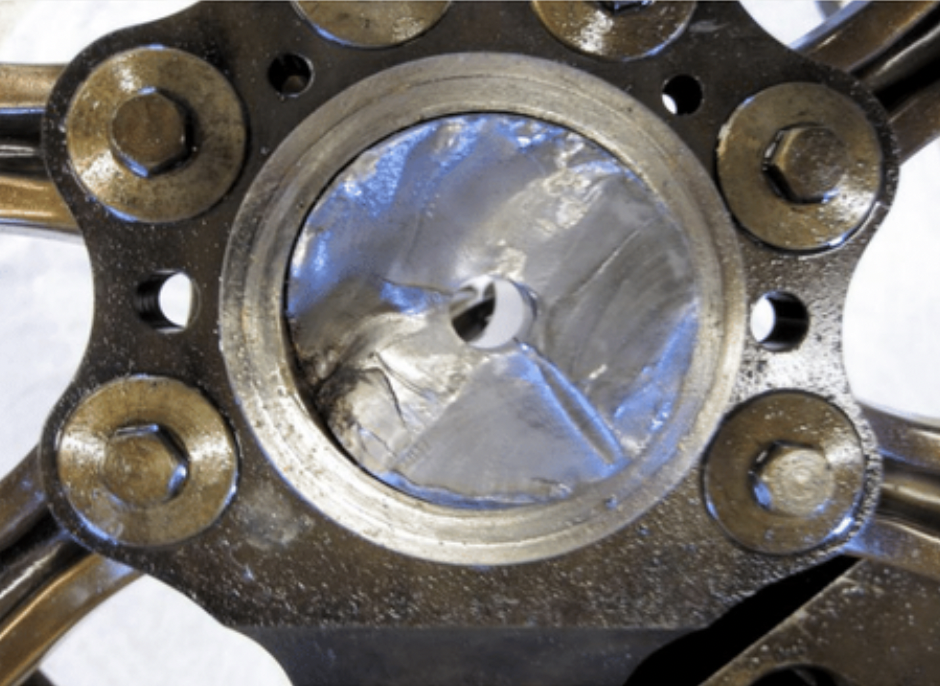
So what are the proper values for propeller nut and thrust nut torque, and how can these high torque values be reached? First, let’s go back to some helpful illustrations from the WWII Lycoming R680-17 Service Manual (Figure 4).
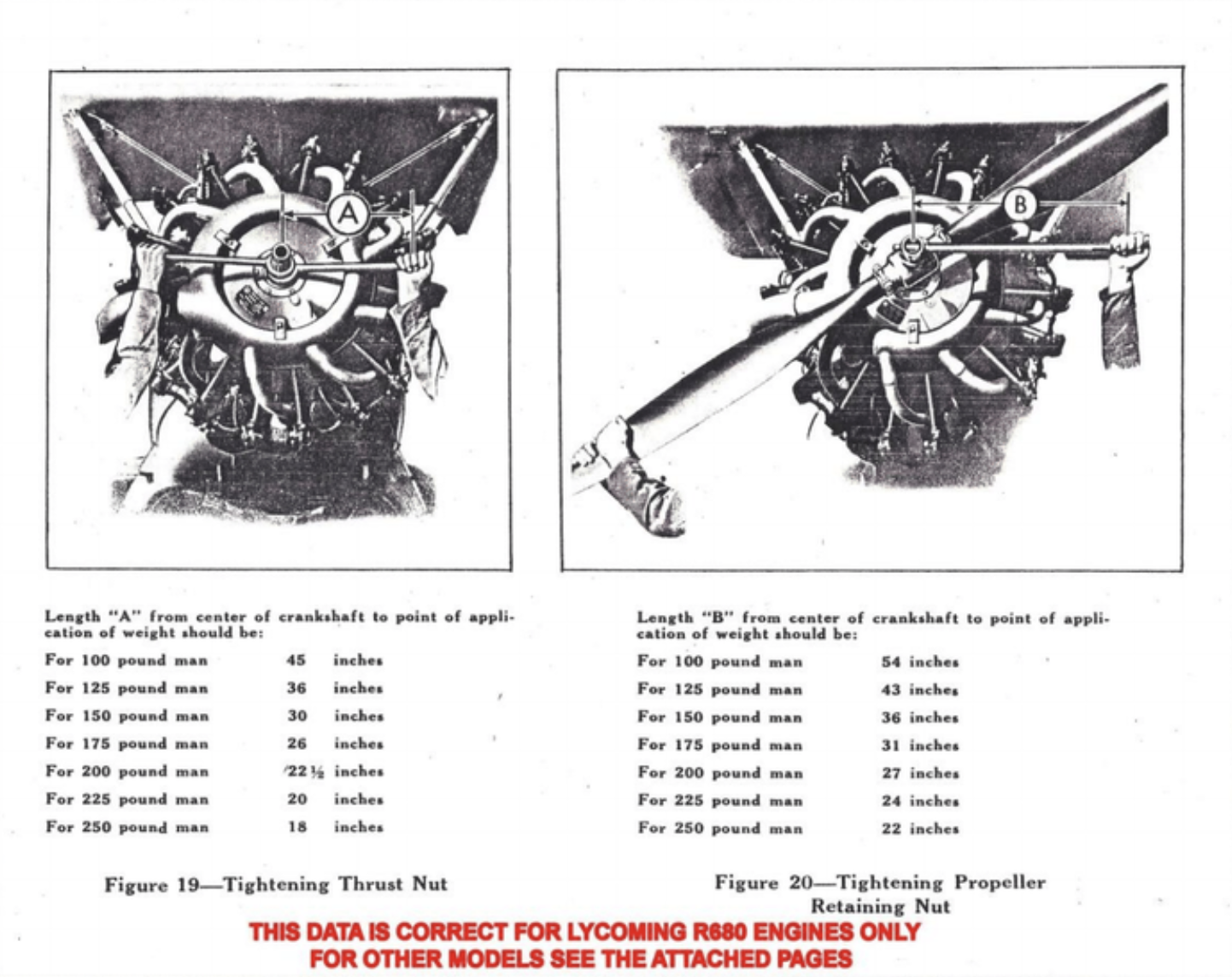
Note that the torque values in this chart are only applicable to that R680 engine. It is the method of tightening the nuts that is of interest to us. In the left photo one man is holding the crankshaft in place as another man is tightening the thrust nut. If the man tightening the thrust nut weighs 125 lbs. and grabs the bar at36” (3 feet) and then hangs all his weight on the bar, the nut will be torqued to 125 x 3 = 375 foot lbs., the proper torque for a Lycoming R680-17 thrust nut.
Likewise in the right photo, if a 225 lb. man grabs the propeller nut bar at 24” (2 feet)and hangs all his weight on the bar, then the propeller will be torqued to 225 lbs. x 2feet = 450 foot lbs., the proper torque for a McCauley propeller on the R680-17. It is an ingenious way to use a person’s body weight to tighten these nuts. It is also possible to make this a one-man job by substituting a ladder for the second man. A scrap of carpet placed on a ladder rung will protect the propeller blade and keep it stationary at the nut is torqued.
The correct distances for where to grab the bar for various engine thrust nuts and propellers are shown below:
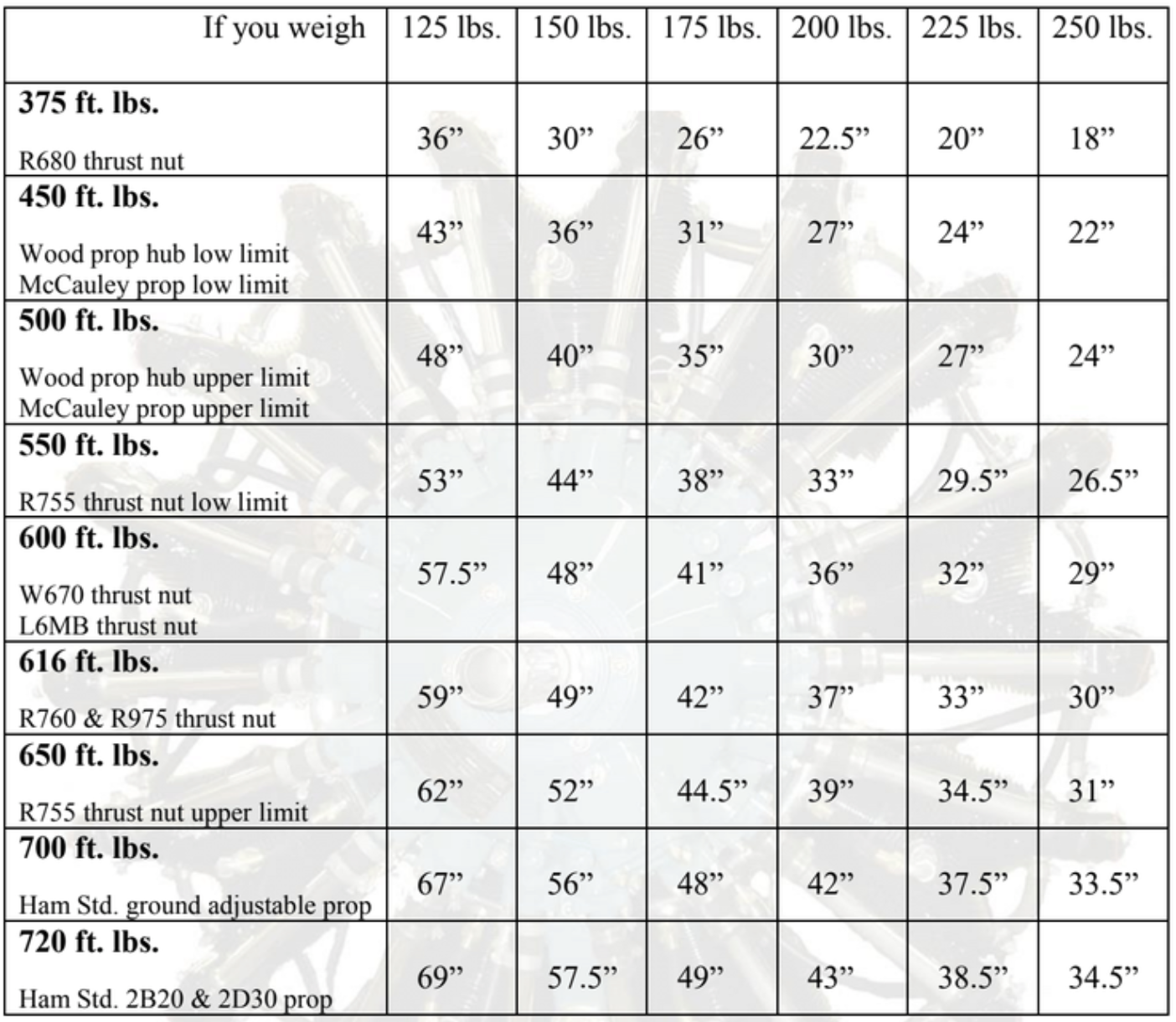
Two nuts that are often neglected in periodic engine inspections are the propeller fastening nut and the engine thrust nut. Both require special wrenches to tighten and loosen them, and maybe for this reason they are overlooked and assumed to be properly torqued. The torque values for each nut is also an order of magnitude greater than any other fastener on the engine. However, along with all the other engine fasteners, these nuts require attention during periodic inspections.
A few years ago an aircraft whose engine that had begun showing ferrous metal in the oil came into our facility. In preparation to remove the engine from the aircraft we first began to remove the propeller. It was then that we discovered that the propeller nut was not tight on the crankshaft. It had been snugged down and safetied, but had not been tightened to the proper torque. The arrows on Figure 1 show wear on the crankshaft splines caused by the propeller chattering on the crankshaft.
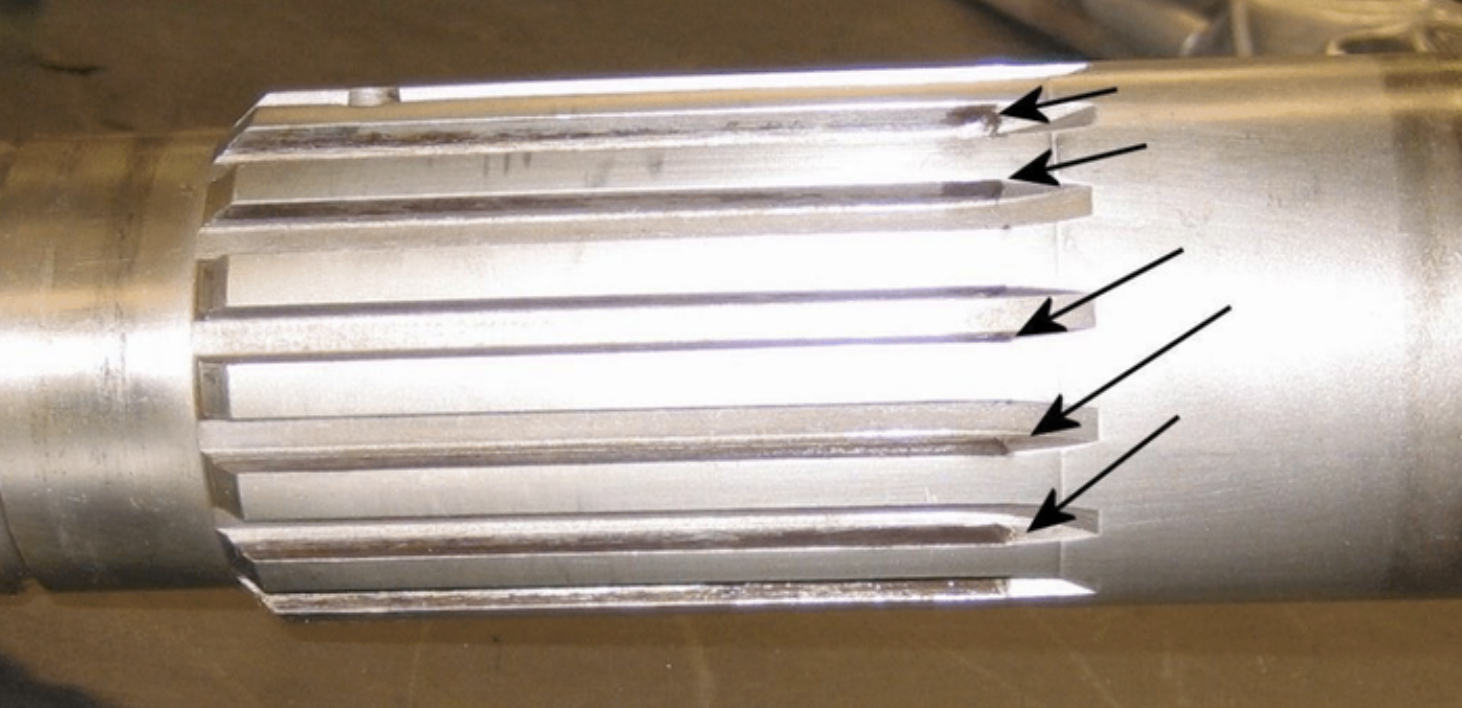
This wear was a cause of rejection for the crankshaft and was a sign of things to come as we continued to disassemble the engine. Figure 2 shows the wear caused on the inner race of the front main bearing by the loose propeller. This wear was the source of the ferrous metal that had been found in the oil.
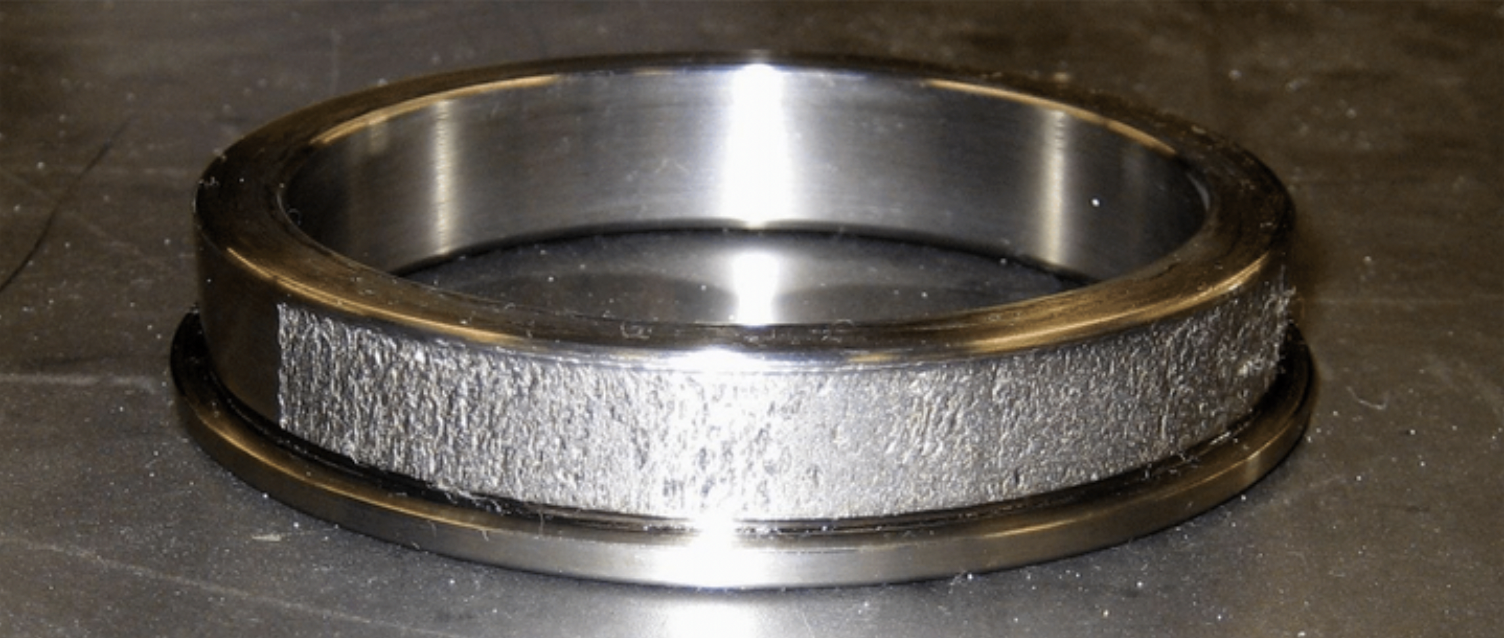
This customer was fortunate that he found the metal in the oil before further damage was done.
On another occasion a different customer experienced a total loss of engine oil pressure in flight. He was able to land the aircraft successfully and upon inspection also found ferrous metal in the oil. When we inspected the engine we noticed that the thrust nut was loose and that the crankshaft could be moved forward and after about .090”. Upon disassembly we found the crankpin had broken in two but was still clamped in the rear half of the crankshaft (Figure 3), underscoring the importance of proper thrust nut torque.
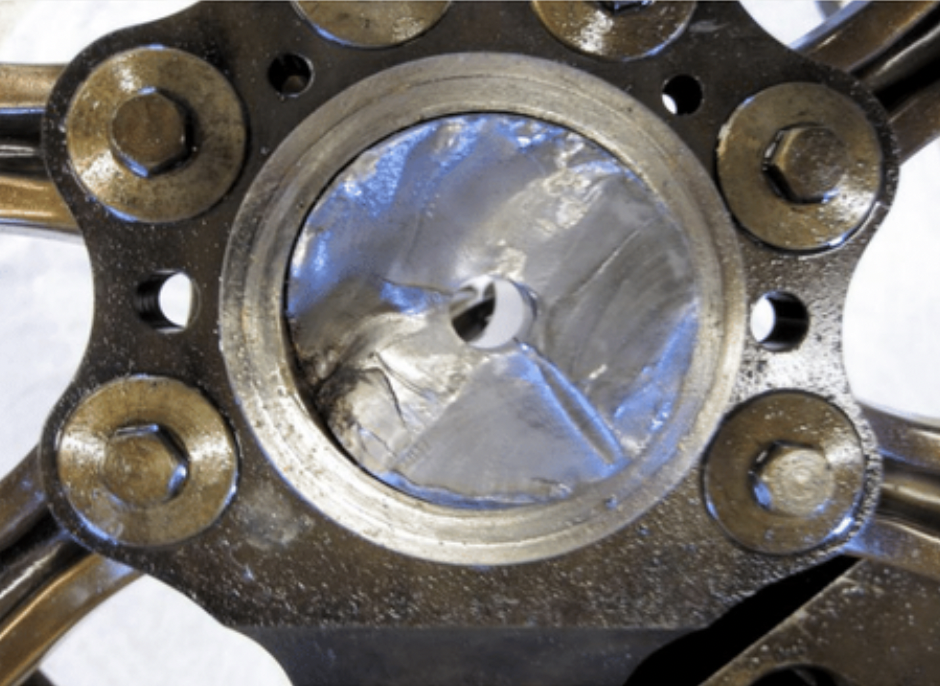
So what are the proper values for propeller nut and thrust nut torque, and how can these high torque values be reached? First, let’s go back to some helpful illustrations from the WWII Lycoming R680-17 Service Manual (Figure 4).
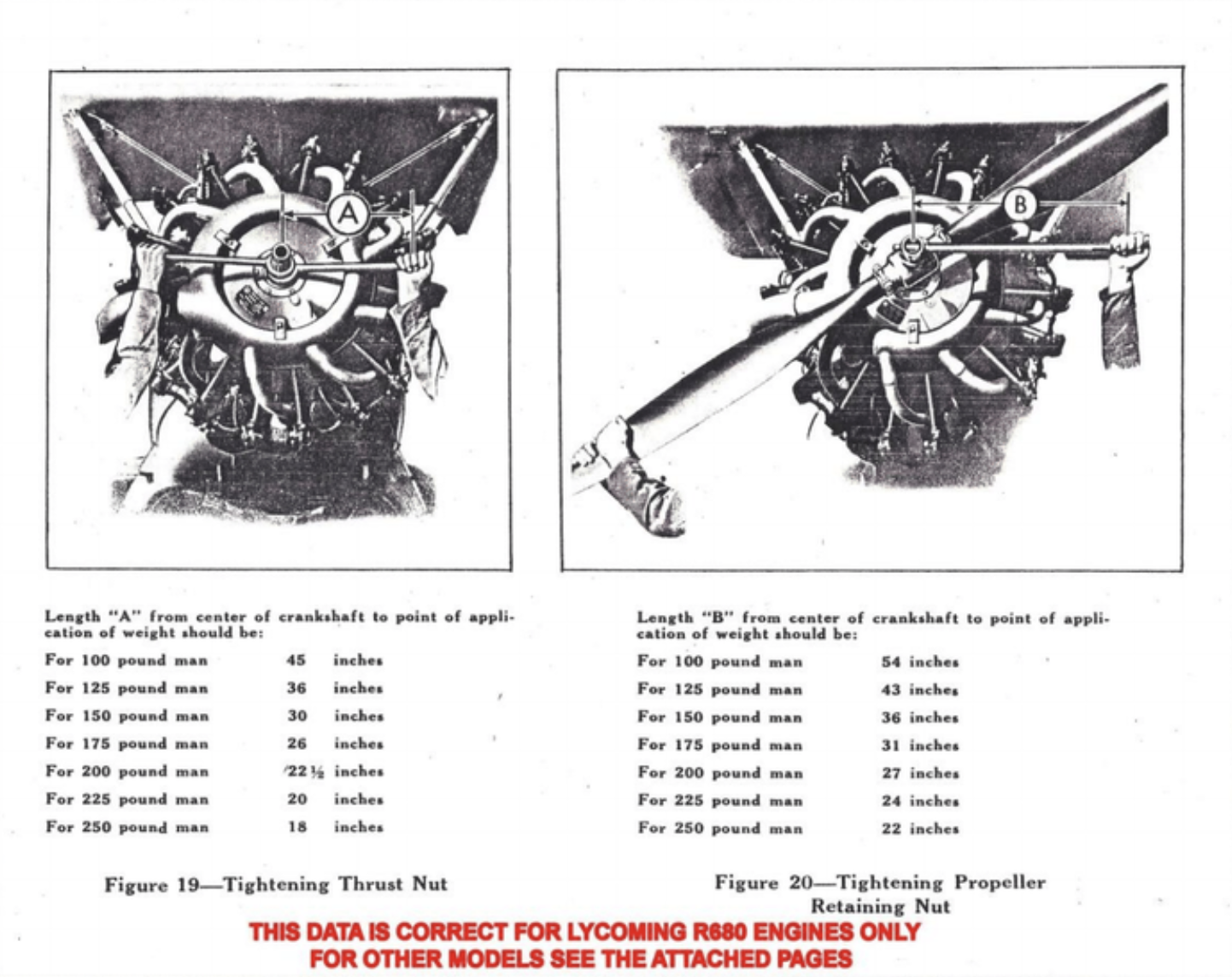
Note that the torque values in this chart are only applicable to that R680 engine. It is the method of tightening the nuts that is of interest to us. In the left photo one man is holding the crankshaft in place as another man is tightening the thrust nut. If the man tightening the thrust nut weighs 125 lbs. and grabs the bar at36” (3 feet) and then hangs all his weight on the bar, the nut will be torqued to 125 x 3 = 375 foot lbs., the proper torque for a Lycoming R680-17 thrust nut.
Likewise in the right photo, if a 225 lb. man grabs the propeller nut bar at 24” (2 feet)and hangs all his weight on the bar, then the propeller will be torqued to 225 lbs. x 2feet = 450 foot lbs., the proper torque for a McCauley propeller on the R680-17. It is an ingenious way to use a person’s body weight to tighten these nuts. It is also possible to make this a one-man job by substituting a ladder for the second man. A scrap of carpet placed on a ladder rung will protect the propeller blade and keep it stationary at the nut is torqued.
The correct distances for where to grab the bar for various engine thrust nuts and propellers are shown below:
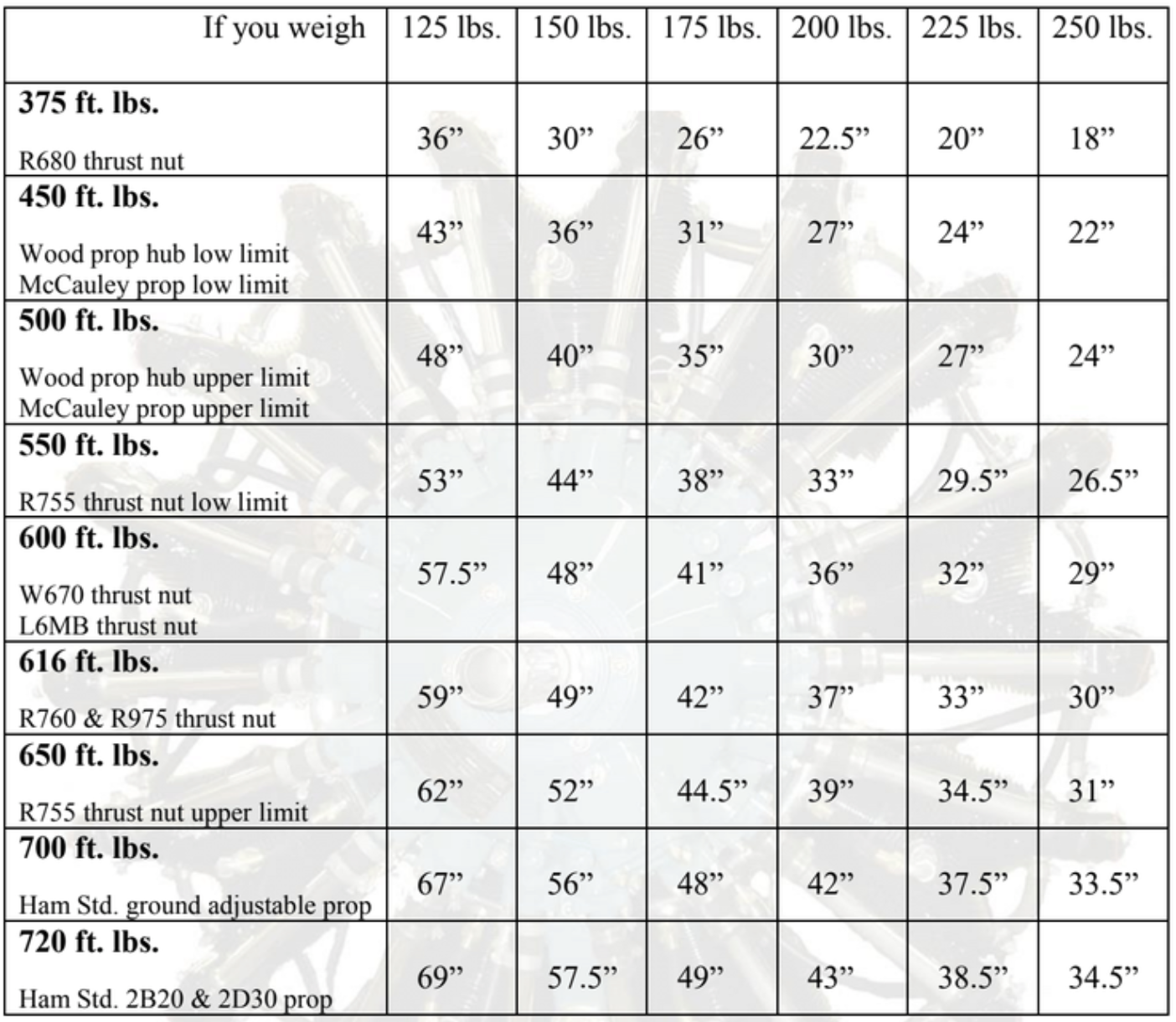