fuel Injection for radial engines
In the 1990s we began to ask the question, “What could be done for these engines that we overhaul and maintain that would increase their performance and reliability?” Though there were several areas which came to mind (ignition system, valve seats, baffles, etc.) we settled on the fuel delivery system as a good place to start. From the beginning, all the small radial engines that we were focused on were supplied fuel through a one-barrel Bendix Stromberg updraft carburetor, primarily NAR6s and NAR7s. The fuel/air mixture was delivered from the carburetor to the cylinders through an induction chamber that was cast integral with the engine power case, then delivered through steel intake pipes to the cylinder heads.
That induction system can be compared to an octopus with tentacles of varying length, some of which are comparatively straight paths from the carburetor (ones feeding the upper cylinders), and others needing to make a sharp turn from the carburetor to the lower cylinders. As a result of the varying lengths of the paths, and the turns (or lack of turns) that the fuel/air mixture must make to reach the cylinders, some cylinders will tend to run rich while others are lean. Therefore, leaning an engine equipped with a carburetor is simply leaning to the leanest cylinder. All the other cylinders are still running rich, resulting in excessive fuel consumption and uneven power production cylinder to cylinder. One cylinder might be producing 42 hp. while another might be only making 38 hp, causing overall engine roughness. It was only after we began to run fuel injected radials that we experienced the turbine-like smoothness that came with fuel injection.
We chose the Jacobs R755-A2 (300 hp.) and R755-B2 (275 hp.) engines as our first models to modify. We already knew that because of the inefficiencies in the induction system design that no two cylinders would be getting the same amount of air. Therefore, our goal in designing a fuel injection system for the Jacobs became to find a way to meter fuel to each cylinder to match the airflow to that cylinder. To replace the carburetor, we chose the Bendix-Precision RSA10 series fuel servos to meter air and fuel, a modified six-cylinder flow divider, Lycoming fuel injection lines, and GAMI fuel nozzles. These nozzles were installed into special fittings welded into the intake pipes.
In the summer of 2004 we ran extensive FAA supervised tests with our first fuel injected Jacobs engine.
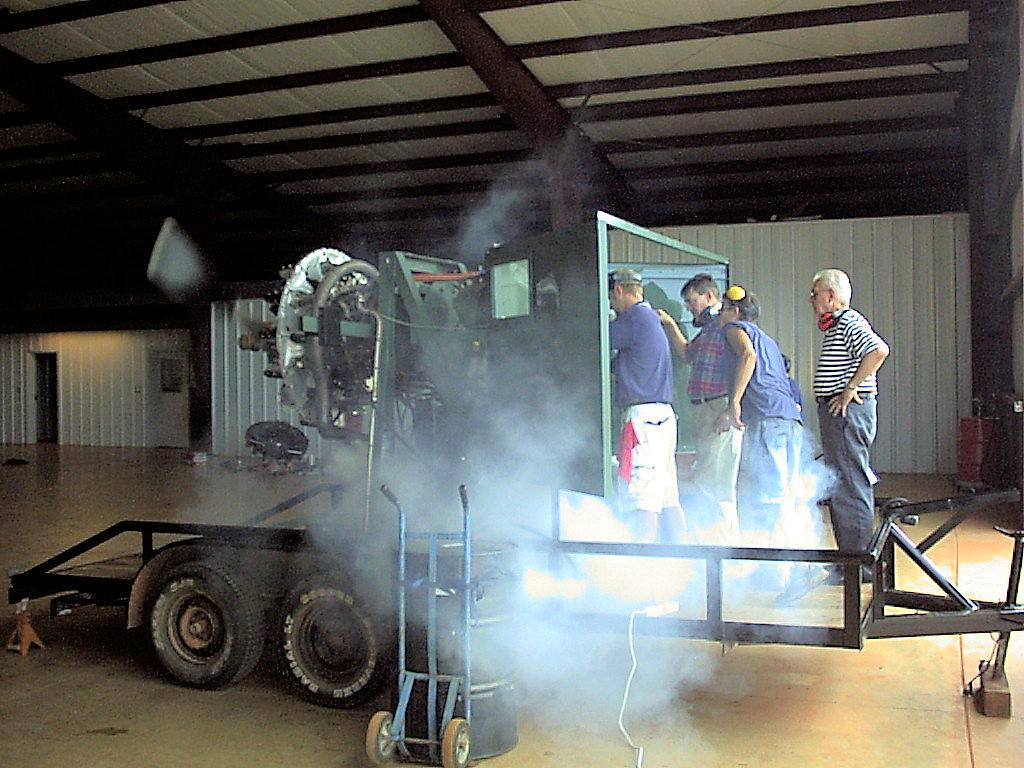
Detonation testing with the FAA
Horsepower calibrations with and without fuel injection, detonation tests, and vibration surveys were done on our dynamometer. We discovered that whereas with the carbureted engine we could not get some of the cylinder exhaust gas temperatures to peak at all, with fuel injection we could make them peak with only a two-second differential. This translated into a fuel savings of 2-3 gph, a significant increase in power, and the smoothest running Jacobs engine we had ever experienced.
As we were waiting for approval on the engine STC we began fitting it to the first aircraft to be approved, a Cessna 195. Again, extensive tests were conducted including a hot fuel test, fuel flow tests
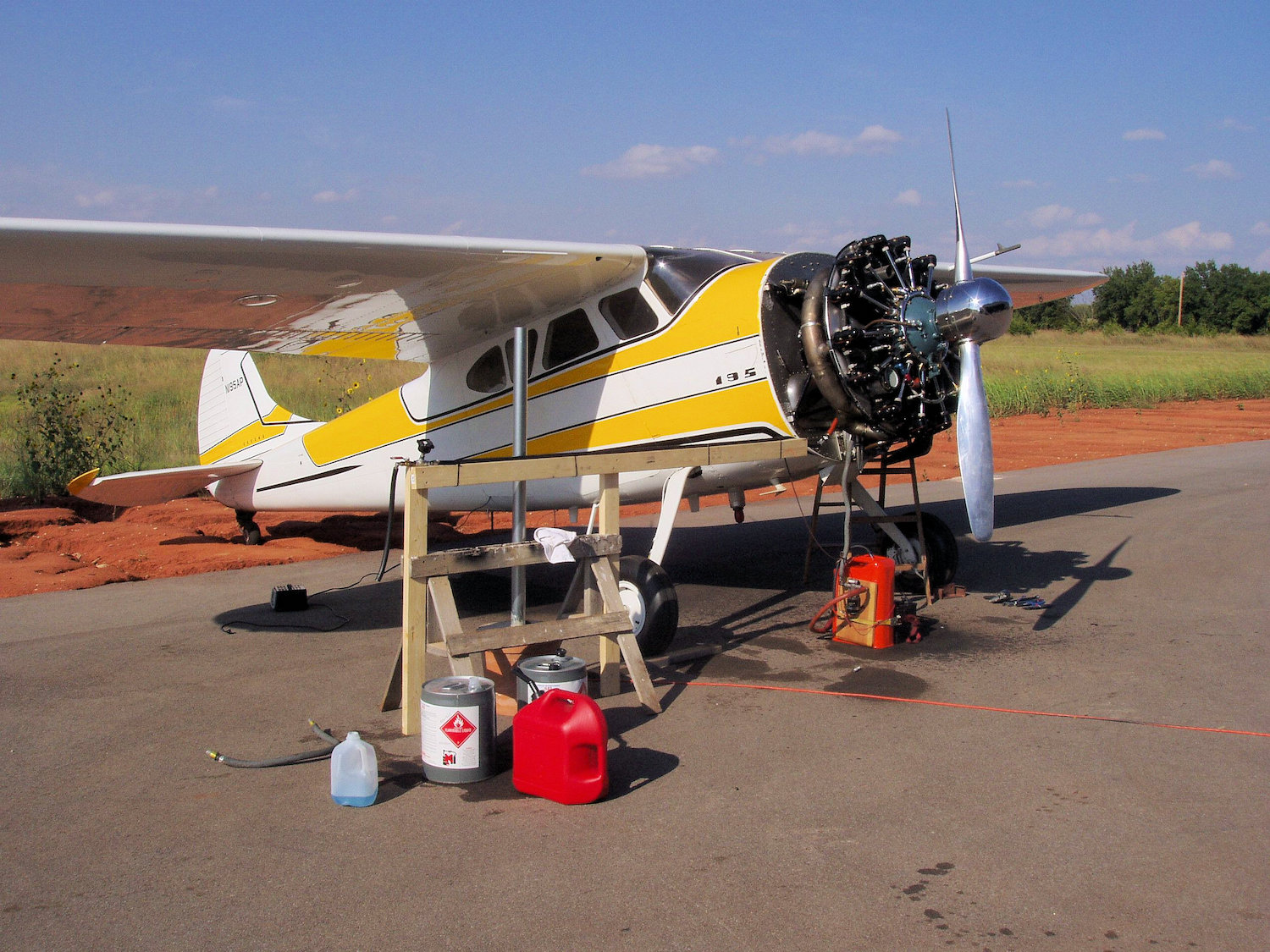
Cessna 195 fuel flow testing
and flight tests. Both the engine and the Cessna 195 STCs were issued before Oshkosh 2004, so to demonstrate its increased range, the 195 was flown nonstop from Tupelo, MS to OSH. Then, just before Christmas that year a fuel injected R755B2 was installed on a WACO Classic YMF-5 and the aircraft went through the same ground tests and flight tests as had been done on the 195.
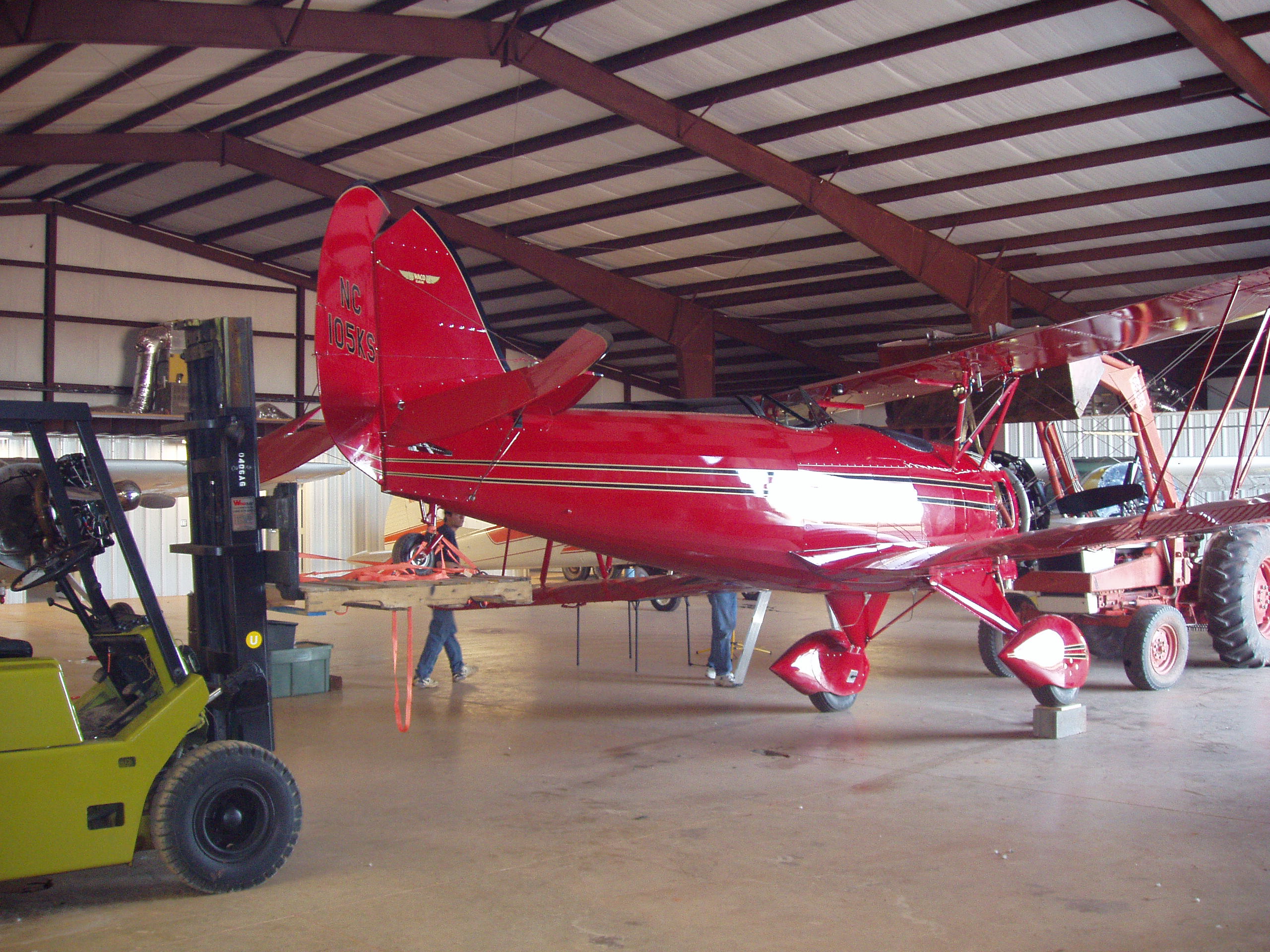
Waco YMF-5 fuel testing (left slip)
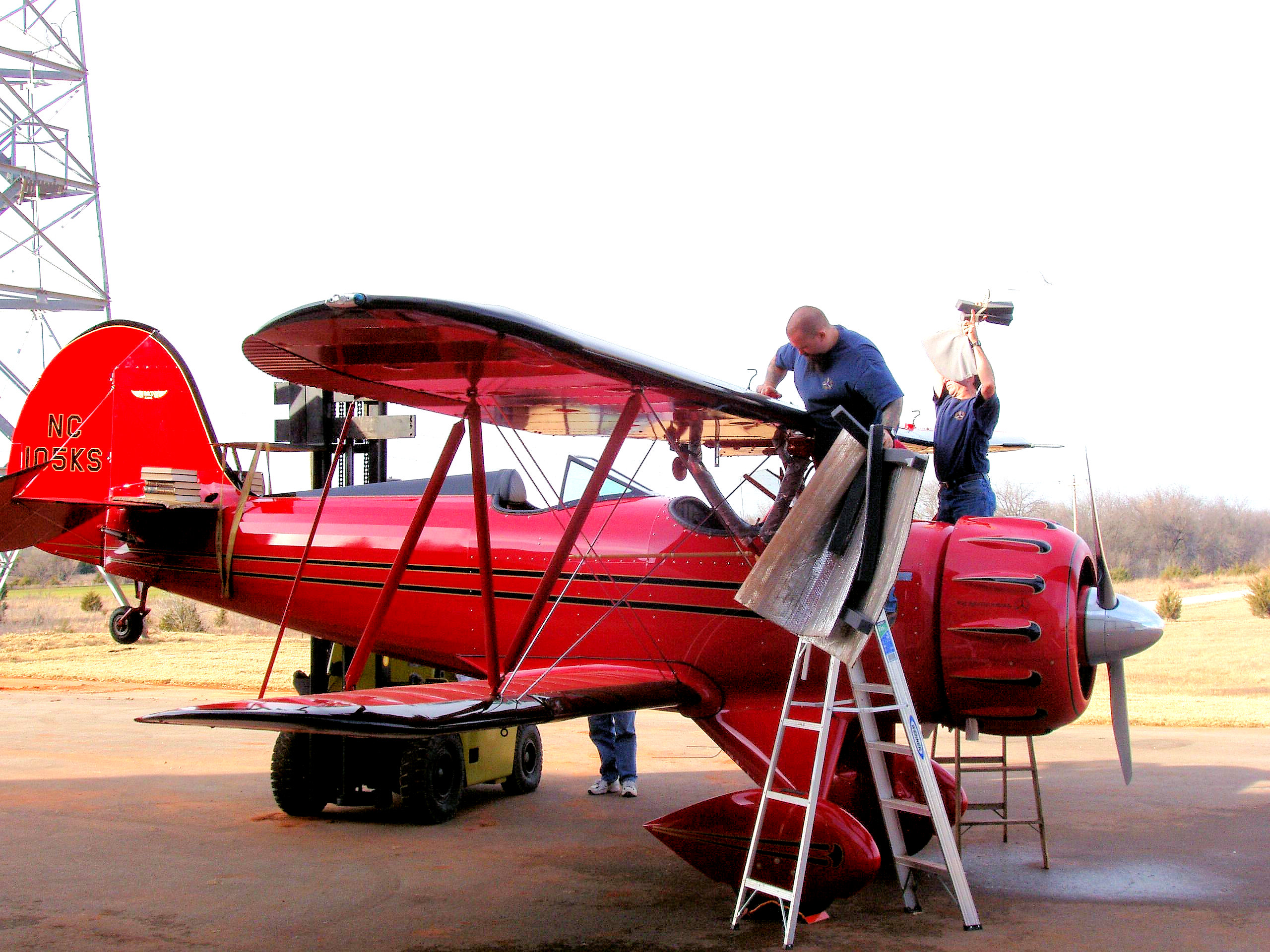
Waco YMF-5 hot fuel testing
All testing was successfully accomplished and shortly thereafter the STC was issued for this aircraft as well. Since that time well over 150 aircraft have been modified with fuel injection, and the list continues to grow.
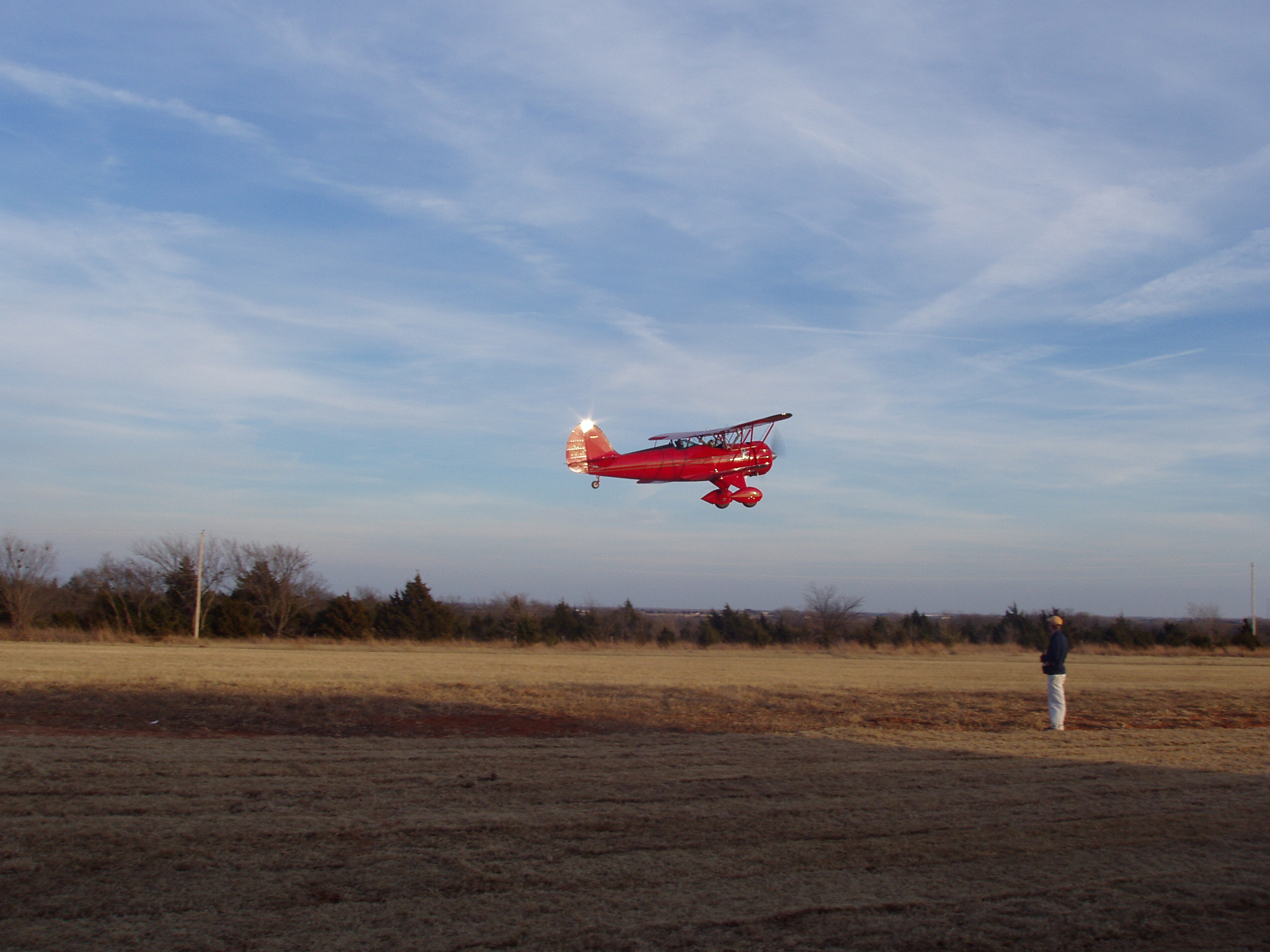
Waco YMF-5 cooling climb test
Fuel injection cowling decal
In 2007 Radial Engines Ltd was granted an STC which approves both a carbureted and fuel injected Jacobs R755 engine on the Boeing Stearman Model 75.
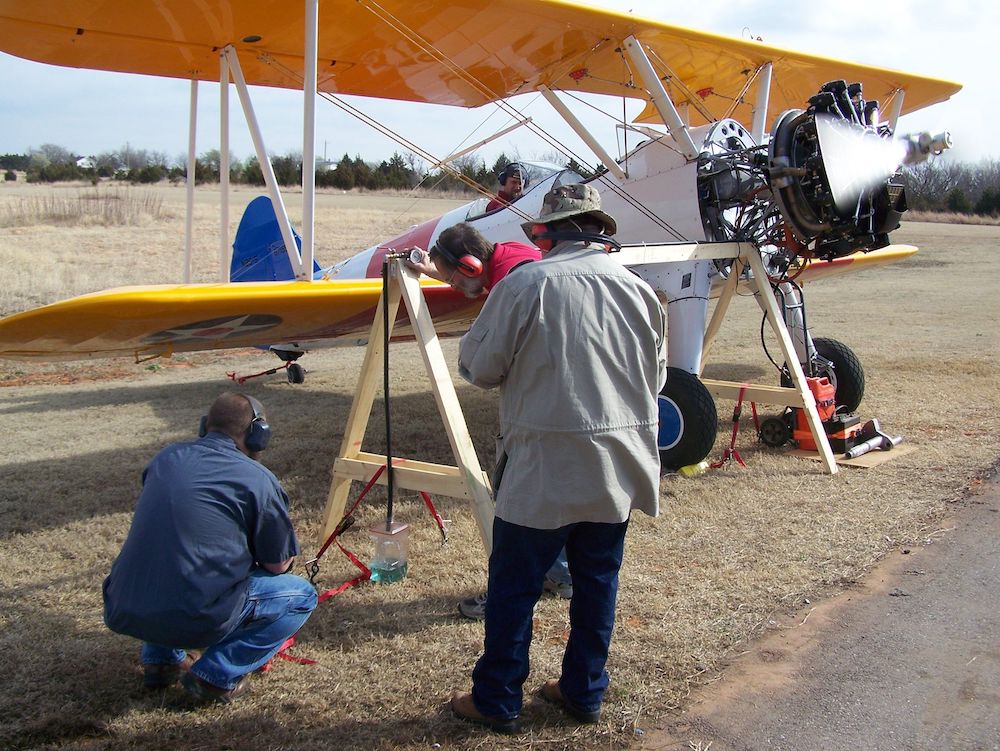
Stearman fuel flow test
With the success of fuel injection on these engines and airframes, several other models of aircraft have since been approved on a one-off basis. A Waco YKC, YKS, several UPF-7s, and multiple Beech Staggerwings now are flying with fuel injected Jacobs engines. A few fuel injected Jacobs L6 engines have also been approved.
One way to view the fuel economy provided by fuel injection is in terms of dollars saved. Another is in terms of the additional range provided. With increased range in view, Radial Engines, Ltd. embarked on a project to fuel inject the Pratt & Whitney R985 engine for the DeHavilland DHC-2 Beaver. Again, the RSA10 fuel servo was used, but a new nine-cylinder flow divider was designed as well as a shuttle valve to transition the engine from ambient air pressure to the engine’s internal supercharger. The conversion was an unqualified success and the fuel injected Beaver showed the same performance enhancements as the previous engines and airframes.
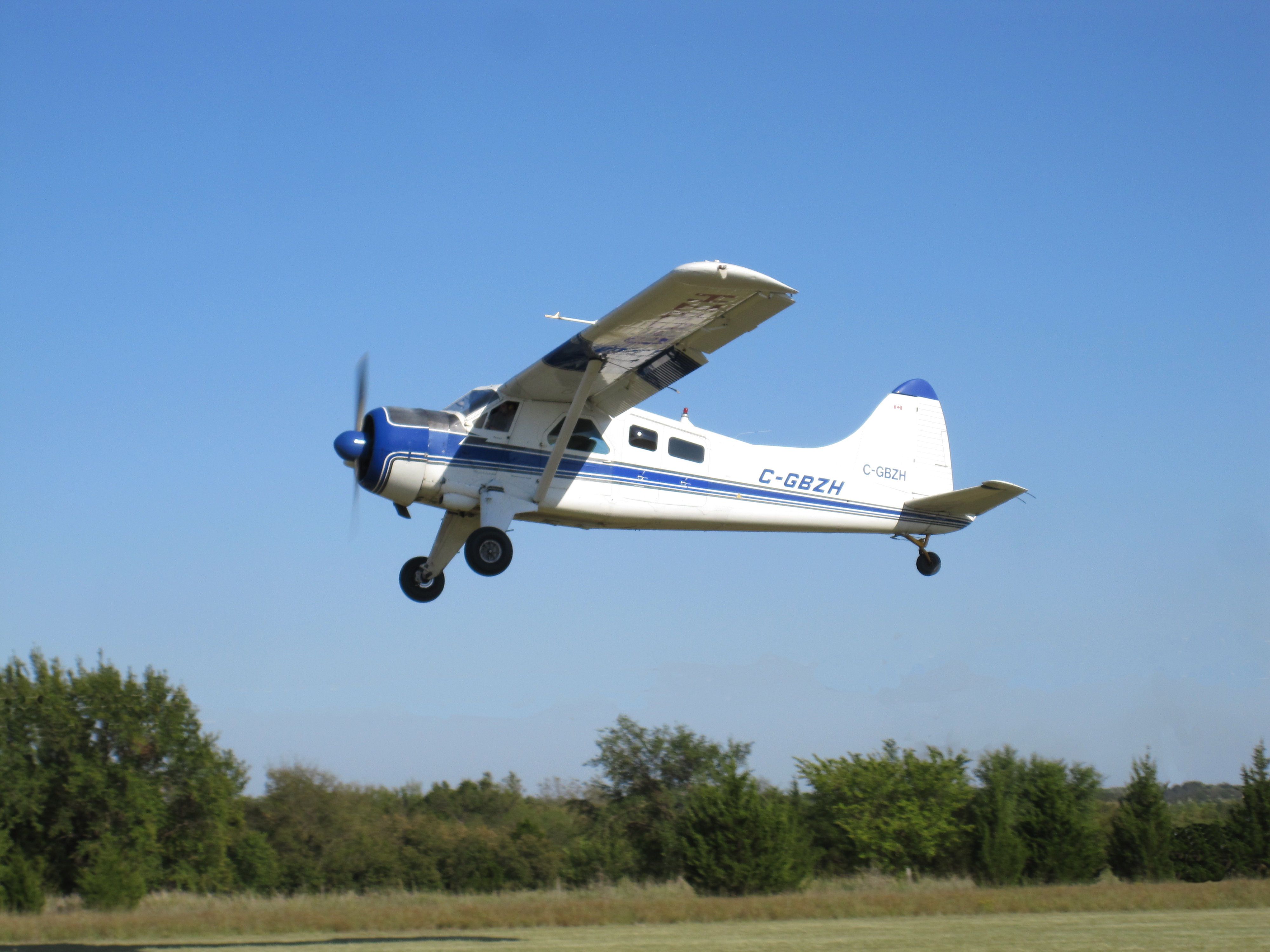
Fuel injected DH-2 Beaver in flight